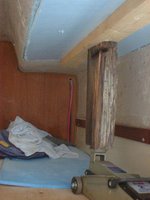
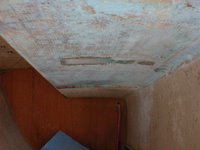
Was a nice day today...a little too nice, as the temperature approached 60 degrees. The Low Temperature Epoxy I have is good from 38 to 60...eek! After sanding the bulk of the old 'blue cheeze' filler off the deck, I test fit the compression fixture to make sure it would hold everything in place while the epoxy cured.
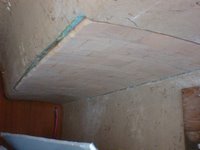
Next was to mix up the Low Temperature Epoxy and prime the surfaces. This was no big deal, but I did notice that the epoxy did not go as far as I thought it would. Oh well. After priming both surfaces, I added the hardener to the BOG mix I made up front by thickening the part A with colloidial silica...I did this so I would not waste time mixing. The mix was not as thick as I wanted, so I had to go back and add more filler. Again, the bog did not go as far as I thought it would. I pasted the boat surface with one batch, and hit the core with another batch. It was no where near the thickness I originally wanted...I ended up with about a millimeter thick layer on everything.
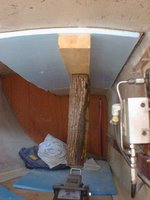
I hope it's enough! It was enough to hold the core in place without support. After sticking the core up, I pressed it in place with a hydraulic jack and a length of 2x4 pressing just the foam board. The thing I made earlier with the luan was too stiff and I needed too much pressure to get it to conform to the seat. The foam ended up working well. I squeezed it gently and just enough to get epoxy to ooze out around the edges a little. After that, I filled some hardware holes on the deck with epoxy to keep the water from getting in to the core. I plan to pull all the hardware eventually....but time limits me and I'm doing the high priority stuff 1st. Oh, BTW, a dixie cup of the Low Temp epoxy with no filler at 60 degrees will get so hot you can't hold the cup!! It is definitely not good unthickened at warm temps.
No comments:
Post a Comment