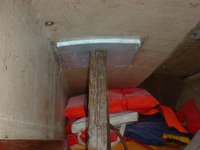
Sunday, January 22, 2006
Started the port side
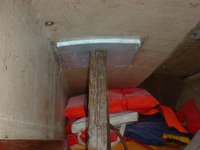
Saturday, January 21, 2006
Final layer of glass / carbon....

New Gauge
Tuesday, January 17, 2006
Backstay Pressure
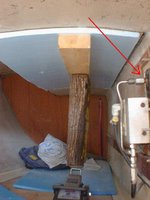
Nice price, quick ship. I'll let you know how it works out.
Monday, January 16, 2006
Added a layer of 14.5 oz glass
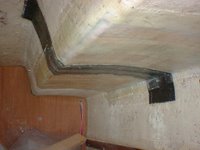
Sunday, January 15, 2006
Skin started
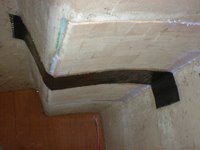
Was blowing blue stink today (40 from the north). Working in the boat on stands made me more nervous than I think I would have been sailing in the same conditions! The core appears to have set well in place. Today I added an 8" 6K carbon fiber strap directly under the traveler. I ran it up the back of the seat and down the seat front. This should give me a little extra strength / less flex in this area where the traveler loads are high. Next will come the layer of 14.5oz glass over the carbon and the rest of the seat, and then a final layer of carbon 3K over the whole thing.
Friday, January 13, 2006
Core Set in Place
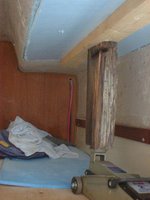
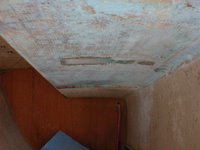
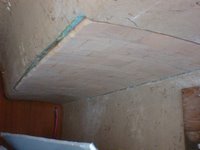
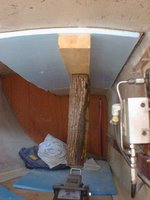
I hope it's enough! It was enough to hold the core in place without support. After sticking the core up, I pressed it in place with a hydraulic jack and a length of 2x4 pressing just the foam board. The thing I made earlier with the luan was too stiff and I needed too much pressure to get it to conform to the seat. The foam ended up working well. I squeezed it gently and just enough to get epoxy to ooze out around the edges a little. After that, I filled some hardware holes on the deck with epoxy to keep the water from getting in to the core. I plan to pull all the hardware eventually....but time limits me and I'm doing the high priority stuff 1st. Oh, BTW, a dixie cup of the Low Temp epoxy with no filler at 60 degrees will get so hot you can't hold the cup!! It is definitely not good unthickened at warm temps.
Monday, January 02, 2006
Some January Progress
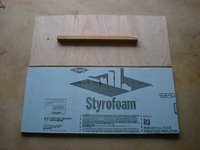
Built the form today to press the balsacore into place once everything else is ready to go. I used 1/2" blue foam board cut as a template for the core material. That was pretty easy. The form is just a section of thin luan plywood cut to size. The idea is to press the core in place into a good epoxy bog and press it with light pressure from a hydraulic jack. It will take the slight curve of the seats from the pressure. The form is covered with polyethelyne plastic and will be reused to hold the skin on during the next step.
Subscribe to:
Posts (Atom)